News & Blog
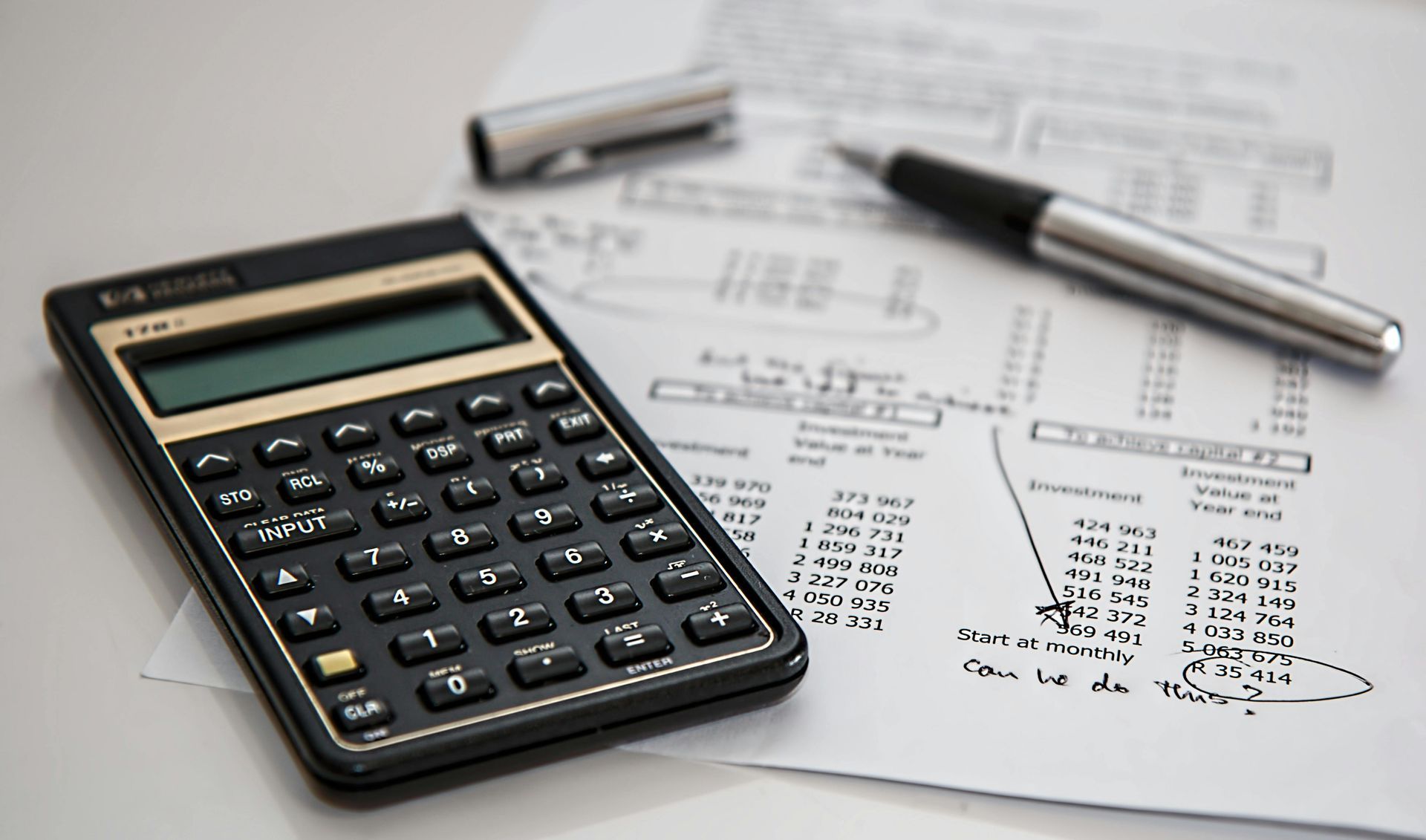
For many QA leaders, the toughest part of getting a digital Quality Management System (‘eQMS’) approved isn’t evaluating the software, it’s justifying the investment to decision-makers who don’t live in the world of audits, deviations, and CAPAs. Unfortunately, many decision-makers often regard QA professionals as cost centers rather than the builders and protectors of brand equity that they are. The overarching key to successfully articulating QA’s value? Stop framing eQMS as a tool that only helps QA do its job. Instead, show how it solves problems across the entire organization . 1. Make it About the Business, Not Just Compliance Executives think in terms of risk, efficiency, and growth. While regulatory readiness is critical, your pitch should connect eQMS to: Faster product release cycles (shorter approval times, less deviations, faster product to market) Lower risk of costly product recalls (and the subsequent brand damage) Smoother market expansion into regulated jurisdictions (leverage tech to standardize processes across newly acquired assets while adhering to state-specific regulations) Product Liability Risk and Insurance costs (the latter of which will decrease as an enterprise’s TCOR (‘total cost of risk’) does down Ultimately, it all comes down to Return On Investment . When leadership sees that eQMS is about protecting revenue and enabling growth, not just checking QA boxes, budget conversations shift. 2. Show the Power of Tech Stack Consolidation Many organizations run separate systems for: EHS (Environmental, Health & Safety) CMMS (Maintenance Management) LMS (Training) Document control (Content Management) PLM (Product Lifecycle Management) A robust, enterprise eQMS can bring all of these under one platform. That means: Fewer vendors to manage Lower subscription and support costs Unified reporting and analytics One source of truth for quality, safety, training, and maintenance records This isn’t just a software purchase, it’s tech stack optimization . 3. Link It to the Cost of Quality Typically, the C-suite only ‘see’ the COGS (Cost of Goods Sold), while having a complete blind spot when it comes to the cost of quality. Poor quality costs money in rework, scrap, downtime, lost sales, and regulatory penalties. A digital QMS: Reduces deviations through real-time monitoring and controlled workflows Prevents repeat issues with faster, more effective CAPA closure Minimizes downtime with integrated maintenance and training records Curries good favor with Regulatory Authorities with complete visibility and trust Lowering the Cost of Poor Quality (CoPQ) directly improves margins, making eQMS a profit protection tool. 4. Build the Business Case with Numbers If possible, quantify: % reduction in manual admin time for QA staff Average hours saved per audit preparation Projected savings from vendor consolidation Estimated CoPQ reduction from better process control When leadership sees ROI on paper, budget approval becomes far easier. Bottom Line An eQMS isn’t “just another QA tool” - it’s a strategic enterprise system that: Consolidates systems Lowers operational costs Protects the brand Enables growth in regulated markets When you frame it this way, budgeting becomes less about cost (control) and more about return .
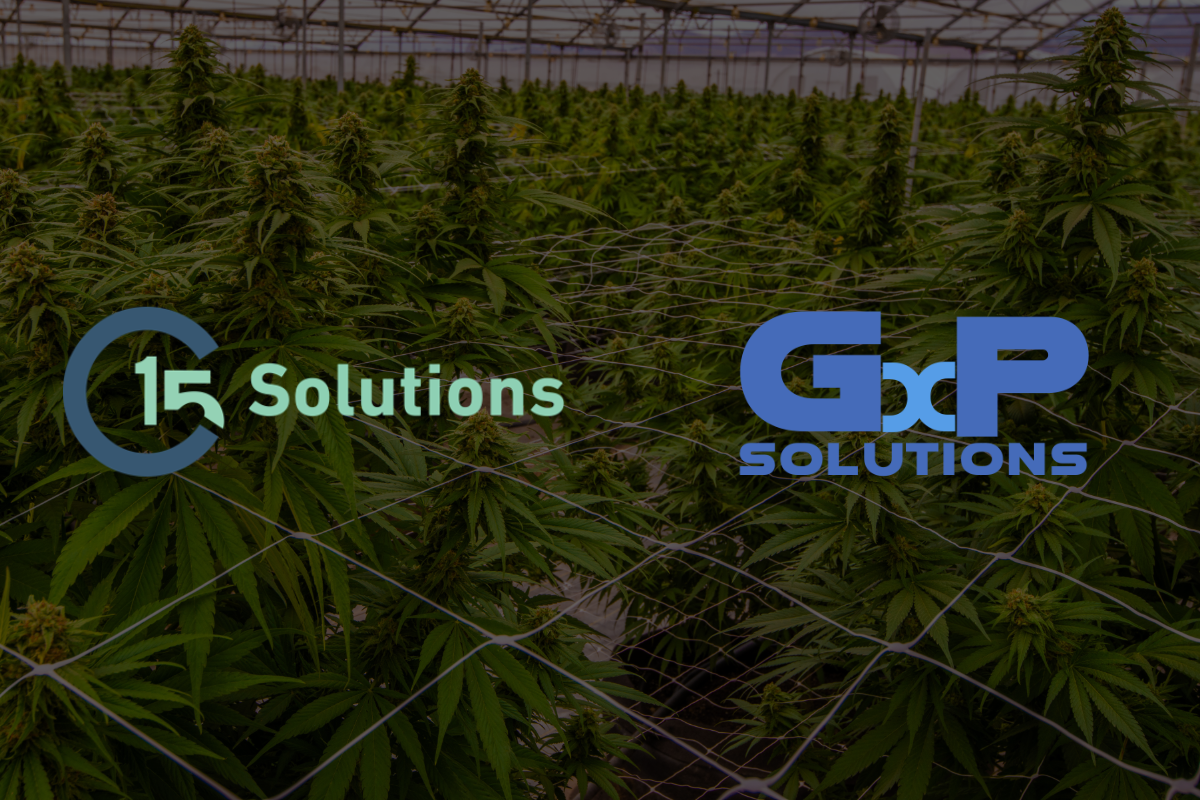
Toronto, ON [7/14/2025] C15 Solutions , a leader in digital Quality Management Systems (eQMS), and GxP Solutions , a trusted provider of GxP compliance consulting and recruiting services for the regulated manufacturers in the cannabis, natural health product, pharma and food sectors, are proud to announce a collaboration partnership. This collaboration combines C15’s validated, cloud-based QMS platform with GxP Solutions’ deep regulatory and operational expertise; C15’s eQMS technology will enable GxP Solutions to more effectively work with mutual clients as well as streamline their quality and compliance processes. “This partnership is about more than software or consulting, it’s about simplifying compliance for companies that operate under some of the most demanding quality and regulatory standards in the world and delivering trusted expertise through cutting edge technology,” said Sean Samuel, VP Sales for C15 Solutions. “We’re excited to pair our hands-on GxP knowledge with a technology platform that enables real-time oversight, audit readiness, and operational efficiency,” said Mandy Wagner, CEO & Founder of GxP Solutions. What It Means for Clients Together, C15 and GxP Solutions will deliver joint service offerings that reduce implementation time, time to market (for new entrants), accelerate regulatory readiness, and help quality teams shift from reactive to proactive, data-based operations. From licensing and validation support to digital transformation of core quality processes, the partnership ensures that clients get both the strategic guidance, and the digital infrastructure needed to thrive in complex regulated markets. Further details on bundled solutions and joint programs will be announced in the coming weeks. About C15 Solutions C15 Solutions delivers a cloud-based, GMP-ready eQMS platform purpose-built for regulated industries. With clients across North America, UK, Europe, Australia and Portugal, C15 transforms enterprise quality. About GxP Solutions GxP Solutions is a Canadian compliance consultancy helping local and global life science and pharmaceutical companies confidently navigate Canadian, U.S., European and Indian GxP regulatory requirements. Our expert team provides end-to-end support across the Quality Management System—including licensing, audits, inspection readiness, process development, training, and operations. We also offer strategic recruiting services tailored to the pharma and life science sectors. With GxP Solutions, experience matters—because it takes one to know one. For media inquiries or partnership opportunities, please contact: Sean Samuel – VP Sales & Marketing sean.samuel@c15solutions.com Mandy Wagner, PMP – CEO/Founder mandy@gxpsolutions.ca www.c15solutions.com | www.gxpsolutions.ca
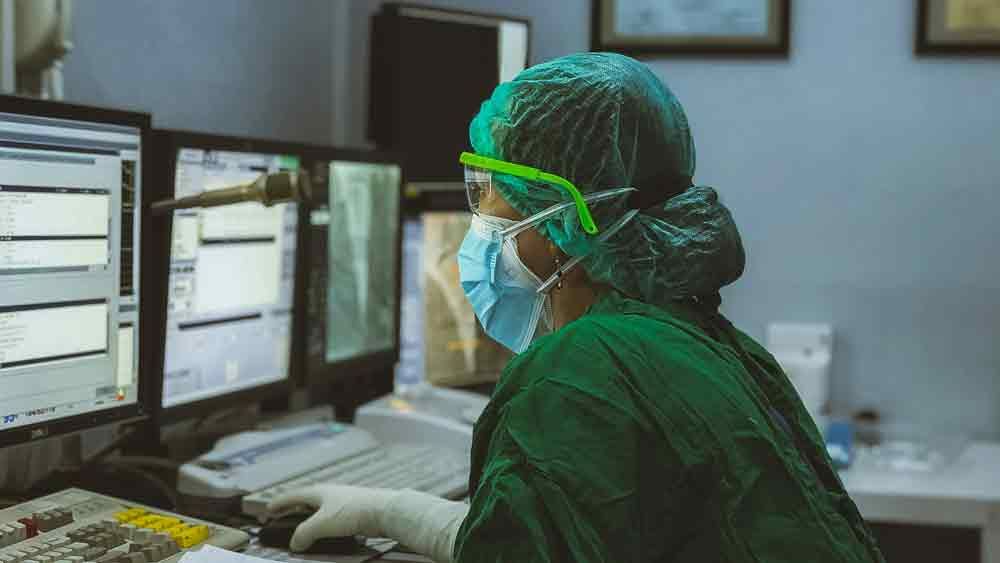
Many companies are still clinging to paper-based and unconnected electronic processes, despite the clear disadvantages. Without modern tools like QMS software, these organizations risk compromising product quality, falling behind in compliance, and ultimately losing competitive ground. In contrast, forward-thinking companies are accelerating their technology adoption. According to Gartner, global IT spending is projected to hit $5.74 trillion in 2025—a 9.3% increase from 2024. Much of this investment is funneled into core business applications such as cloud platforms, cybersecurity, and enterprise systems—includin g QMS software designed to modernize and streamline quality management. Read full article by Stephanie Ojeda
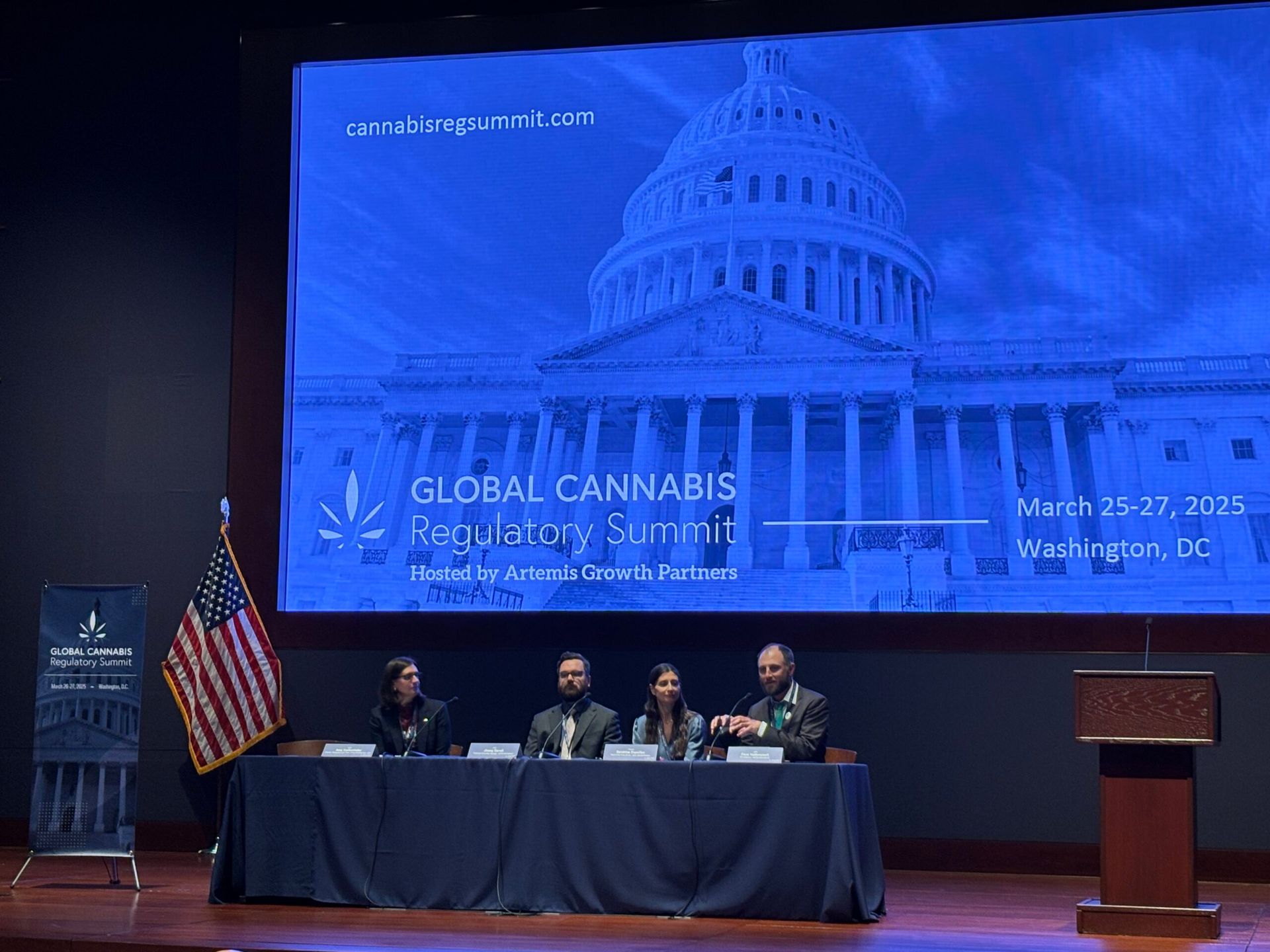
At the inaugural Global Cannabis Regulatory Summit in Washington, D.C., leaders from 17 countries gathered to tackle the challenges facing the cannabis industry. Central topics included the urgent need for global standardization, clearer distinctions between medical and adult-use markets, the industry's responsibility to lead with science, and the widespread educational gaps across healthcare, regulatory, and consumer sectors. The event emphasized collaboration between standards organizations and industry stakeholders to build a more harmonized and trusted global cannabis framework. Read full article by David Vaillencourt.
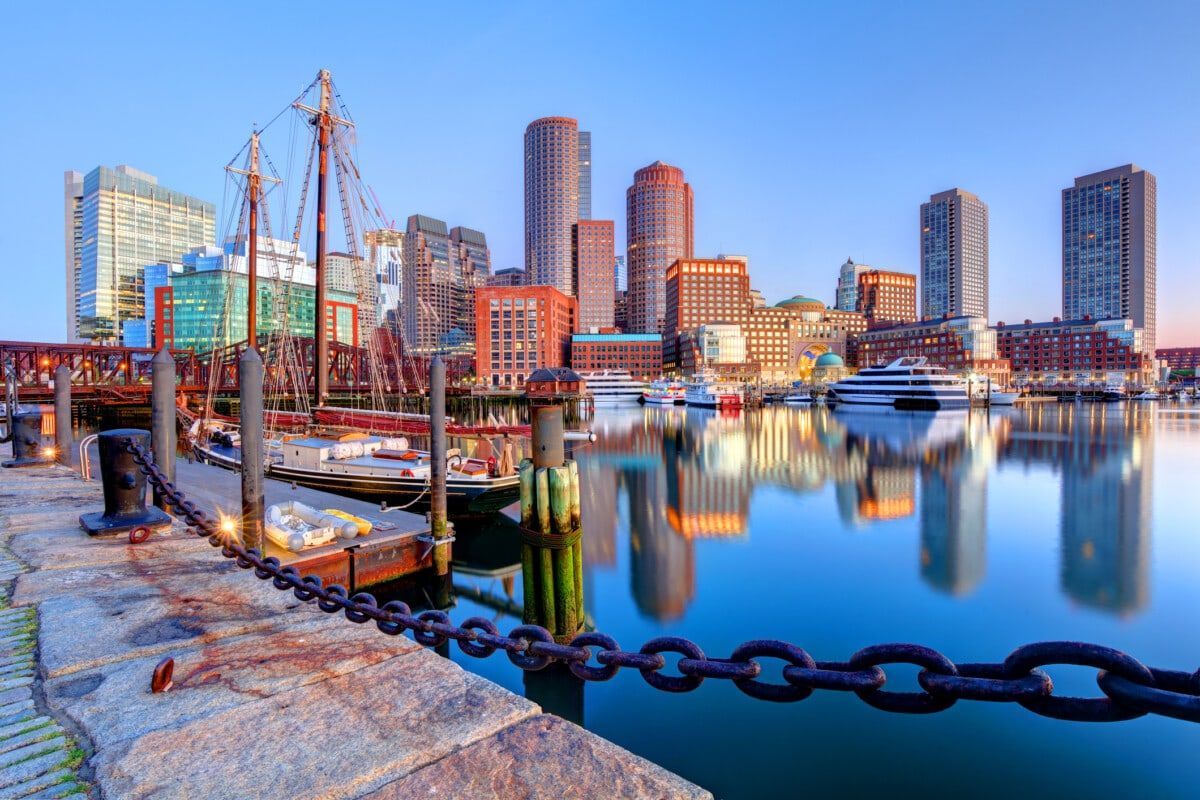
Massachusetts cannabis cultivators and product manufacturers are required to implement a Quality Management System (QMS) to comply with state regulations and ensure product safety, consistency, and accountability. Under 935 CMR 500.105 and 935 CMR 500.120 , the Cannabis Control Commission (CCC) outlines strict operational requirements, including written procedures, quality controls, and recordkeeping protocols. For cultivators and manufacturers, a robust QMS isn’t just about staying compliant—it’s the backbone of sustainable, high-performing operations. Key Aspects of QMS Implementation for Cultivators and Manufacturers 1. Standard Operating Procedures (SOPs) Per 935 CMR 500.105(1), licensees must develop and maintain SOPs that govern cultivation, production, sanitation, waste disposal, security, and packaging. For example: Cultivators need SOPs for pest management , nutrient schedules , batch tracking , and environmental controls . Manufacturers must document procedures for extraction , infusion , post-processing , and cleanroom operations . These SOPs are central to your QMS and serve as the foundation for consistent, compliant operations. 2. Product Testing and Quality Assurance Under 935 CMR 500.160, all marijuana and marijuana products must be tested by Independent Testing Laboratories (ITLs) before sale. Your QMS should ensure: Documentation of batch samples, chain of custody, and lab reports. Quality hold procedures for quarantining untested or failed product batches. Review protocols for assessing lab results and determining corrective actions. 3. Corrective and Preventive Actions (CAPAs) Non-conformances, whether related to equipment, processes, or test failures, require documented responses under your QMS. According to 935 CMR 500.105(1)(l), you must maintain a process for handling complaints and adverse events, which often tie directly into your CAPA program. A good CAPA workflow includes: Root cause analysis. Assignment of responsibility. Timelines for resolution. Documentation of resolution and effectiveness verification. 4. Employee Training and Competency Under 935 CMR 500.105(1)(m), all personnel must be trained in their respective job functions, including sanitation, safe handling, and emergency procedures. Your QMS should manage: Training schedules and content. Role-based competency checklists. Electronic records of training completion and recertification dates. 5. Audit Readiness and Internal Reviews To stay inspection-ready, your QMS should include periodic internal audits and quality reviews. While not explicitly required in regulation, internal auditing supports compliance with 935 CMR 500.105 by identifying potential gaps before a CCC inspection occurs. Why Cultivators and Manufacturers Need a QMS ✅ Regulatory Compliance With the CCC increasing oversight and license renewals now tied to operational reviews, a well-documented QMS ensures you meet 935 CMR 500.105, 500.120, and 500.160 requirements. ✅ Product Safety and Consistency From crop to concentrate, maintaining batch traceability, test result integrity, and label accuracy is key to delivering reliable, compliant products to consumers. ✅ Operational Efficiency Standardized workflows, automated documentation, and streamlined training reduce downtime, minimize rework, and support scale. ✅ Risk Mitigation A QMS provides visibility into recall protocols, deviation logs, and incident trends, helping your team prevent future issues before they impact compliance or product quality. Staying Competitive in Massachusetts' Evolving Cannabis Market With over $5 billion in sales and increasing competition, Massachusetts cultivators and manufacturers must go beyond regulatory minimums. Implementing a digital QMS not only satisfies CCC expectations—it helps you: Scale production while maintaining quality Prepare for multi-state expansion with audit-ready documentation Support branding with verified product consistency and safety Whether you’re managing a canopy or a kitchen, building your business on a QMS framework is one of the smartest investments you can make. Want to explore how a QMS purpose-built for cannabis operators can support your team in Massachusetts? Ask us for a demo.
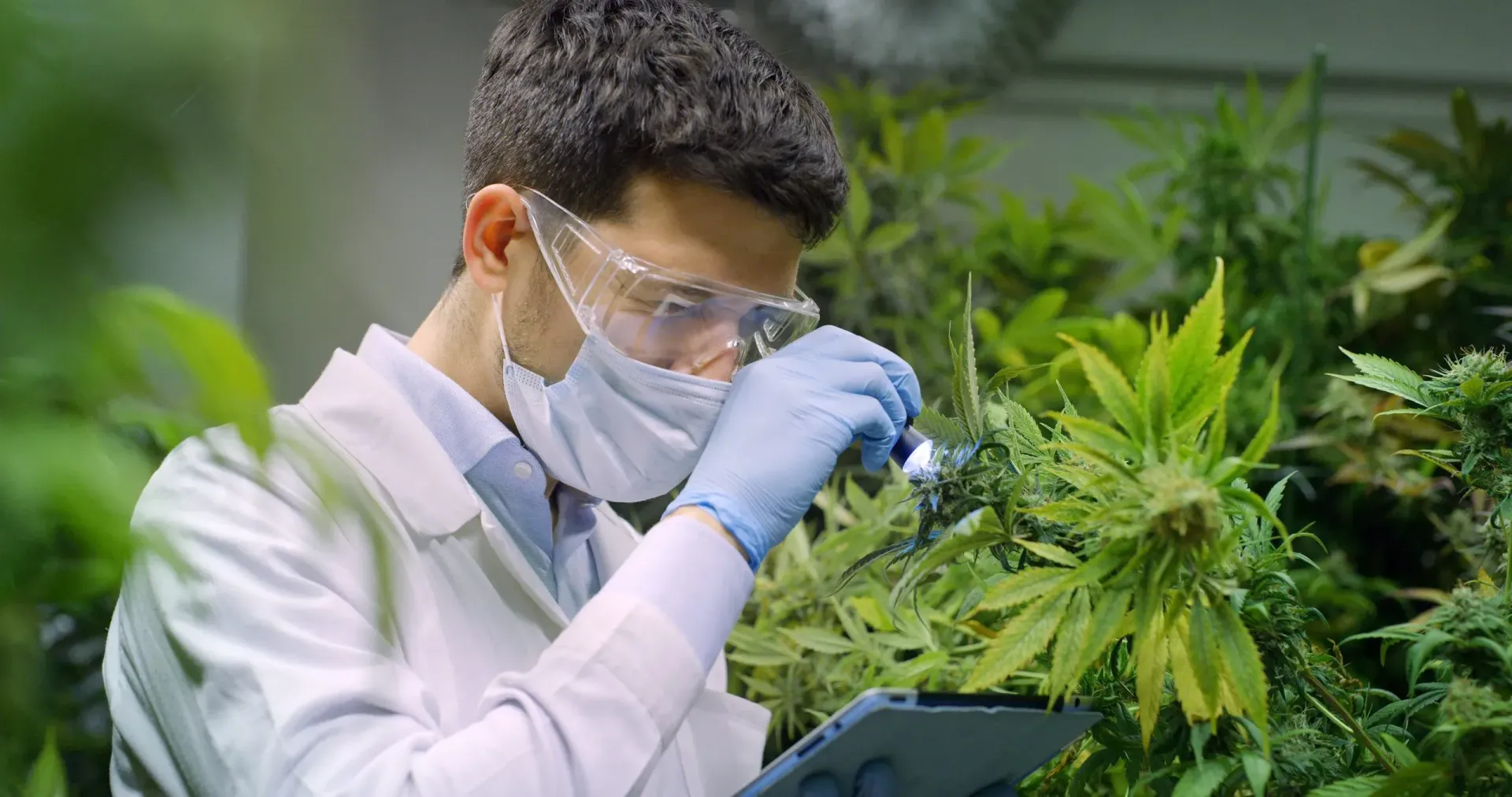
In Missouri, the implementation of a Quality Management System (QMS) is a critical requirement for cannabis production facilities, as outlined in the state's regulations. The purpose of a QMS is to ensure that facilities maintain high standards of quality and compliance throughout their operations. Below, we will provide a detailed overview of the QMS requirements, including the regulatory framework, implementation guidelines, and practical implications for licensees. Regulatory Framework The requirement for a QMS is specified in 19 CSR 100-1.100(4)(D), which mandates that all licensees implement a QMS using a published standard within one year of receiving department approval to operate. The chosen standard must be applicable to the facility type and emphasize regulatory compliance. Acceptable standards include those offered by recognized organizations such as the International Organization for Standardization (ISO), ASTM International, Cannabis Safety and Quality, or the Foundation of Cannabis Unified Standards. Implementation Guidelines Selection of a Standard: Licensees must select a QMS standard that aligns with their specific operations. For example, ISO 9001 is a widely recognized standard that focuses on quality management principles, including customer focus, leadership, and continual improvement. Documentation and Procedures : The QMS must include comprehensive documentation of all processes and procedures. This includes standard operating procedures (SOPs) for cultivation, manufacturing, and distribution, as well as protocols for handling non-conformities and corrective actions. Training and Competency : Employees must be trained on the QMS and demonstrate competency in their roles. This ensures that all staff members understand the quality standards and their responsibilities in maintaining compliance. Monitoring and Measurement : Facilities must establish systems for monitoring and measuring key performance indicators related to quality. This includes regular audits, inspections, and testing to ensure that products meet safety and quality standards. Continuous Improvement : A core component of the QMS is the commitment to continuous improvement. Facilities must regularly review their processes and make necessary adjustments to enhance quality and efficiency. Practical Implications for Licensees Regulatory Compliance: Implementing a QMS helps ensure compliance with Missouri's cannabis regulations, reducing the risk of violations and penalties. It also prepares facilities for inspections and audits by regulatory bodies. Product Quality and Safety : A robust QMS enhances product quality and safety, which is crucial for consumer trust and market competitiveness. It ensures that products are free from contaminants and meet all labeling and packaging requirements. Operational Efficiency : By standardizing processes and procedures, a QMS can improve operational efficiency, reduce waste, and lower production costs. This can lead to increased profitability and sustainability for the business. Risk Management : A QMS provides a framework for identifying and mitigating risks associated with cannabis production. This includes risks related to product recalls, supply chain disruptions, and regulatory changes. Scenario-Based Example Consider a cultivation facility that has recently received its license to operate. To comply with the QMS requirement, the facility selects ISO 9001 as its standard. The facility then develops SOPs for each stage of the cultivation process, from seed selection to harvest. Employees undergo training to understand these procedures and their role in maintaining quality. The facility also implements a system for regular testing of soil and water quality, as well as environmental conditions such as temperature and humidity. By continuously monitoring these factors, the facility can quickly identify and address any issues that may affect product quality. Summary In summary, the implementation of a Quality Management System is a mandatory requirement for cannabis production facilities in Missouri. It involves selecting an appropriate standard, documenting processes, training employees, and continuously monitoring and improving operations. A well-implemented QMS not only ensures regulatory compliance but also enhances product quality, operational efficiency, and risk management. As regulations evolve, facilities must remain adaptable and committed to maintaining high standards of quality and compliance.
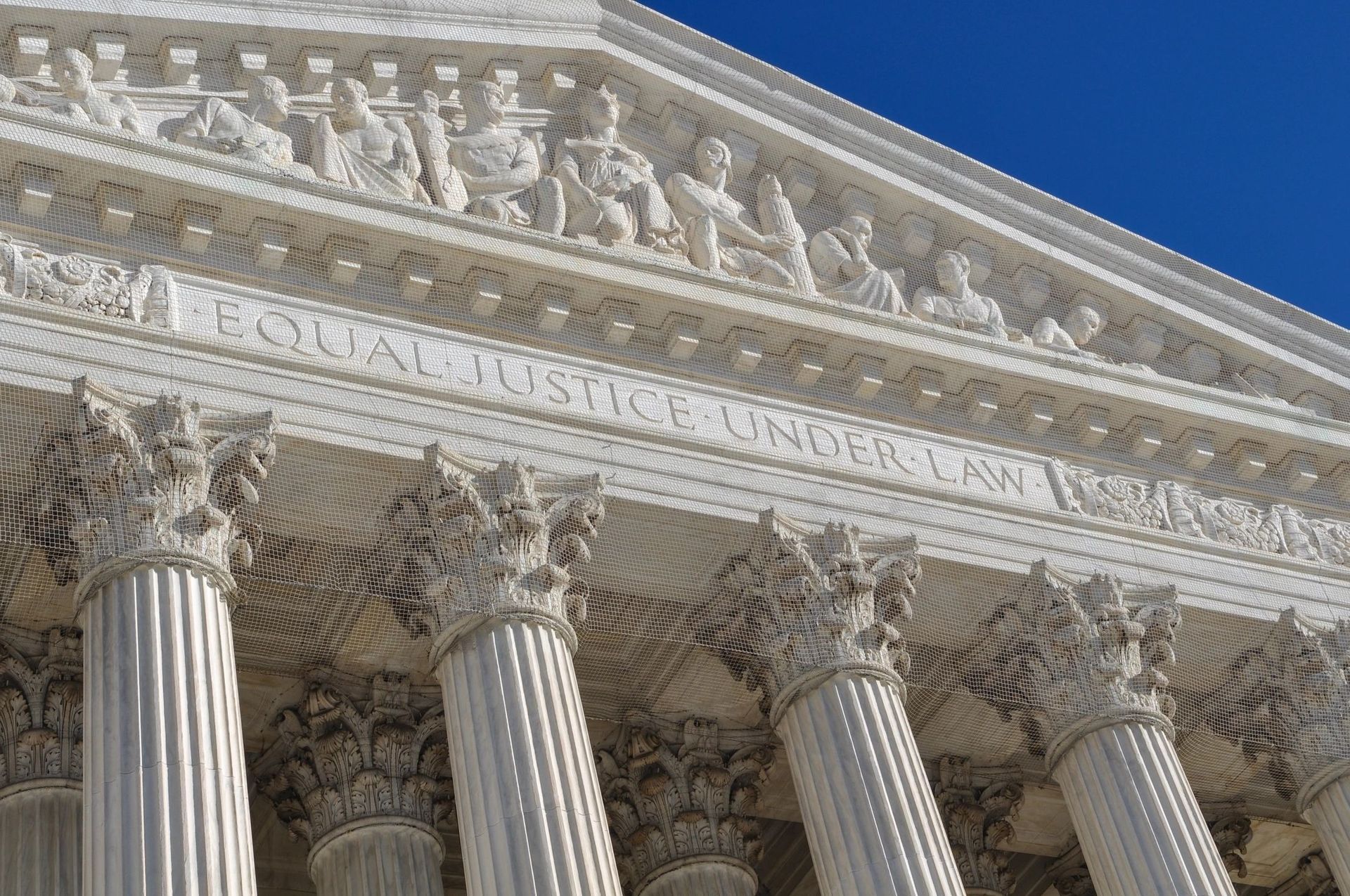
Navigating the Cannabinoid Safety and Regulation Act (CSRA): A Call to Action for Industry Standards
Originally posted by David Vaillencourt, CEO, The GMP Collective September marked a pivotal moment for the cannabis and hemp industries. Senator Ron Wyden introduced the Cannabinoid Safety and Regulation Act (CSRA), reinforcing the industry’s move toward federally mandated safety standards. Simultaneously, the National Academies of Sciences, Engineering, and Medicine (NASEM) released a comprehensive report emphasizing the urgent need for standardized practices . The message is clear: compliance with Good Manufacturing Practices (GMPs) and ASTM International standards is no longer a nice to have—it is the bare minimum to ensure product credibility and safety. The CSRA: Reinforcing the Path Forward While the CSRA doesn’t establish new precedents, it significantly reinforces what industry advocates and previous legislative efforts have been emphasizing: the necessity for standardized safety and quality practices in cannabinoid products. This alignment with global regulatory practices brings the cannabis and hemp industries in line with how other consumer products are regulated worldwide—through adherence to GMPs. Key highlights of the bill include: Mandatory GMP Compliance : All products must be manufactured in facilities adhering to GMP standards, ensuring consistency and safety. ASTM Standard Symbol Requirement : Products containing intoxicating cannabinoids must display the ASTM standard symbol , promoting transparency and uniformity . Facility Registration and Inspection : Enhanced oversight through mandatory facility registration and regular FDA inspections. Comprehensive Labeling : Strict labeling requirements to provide accurate consumer information. Emphasizing Standards in the NASEM Report In tandem with legislative developments, the NASEM report titled “Cannabis Policy: Public Health and Health Equity” underscores the critical need for standardized practices. The report calls for increased education, research, and the adoption of established standards to ensure product safety and efficacy. The report calls for adoption of monographs (a type of standard) published by the U.S. Pharmacopeia (USP), who works closely with ASTM’s Cannabis Committee on developing model standards for the industry. As the Vice-Chair of the ASTM D37 Committee on Cannabis , I’ve witnessed firsthand the dedication to creating robust standards that address both quality and safety across all aspects of cannabis and hemp products. “Many C15 customers understand that integrating GMP and ASTM standards into their quality programs today is not only essential for compliance but also key to long-term growth and success,” says Sean Samuel of C15 Solutions , an eQMS solution provider for the cannabis industry. “By acting now, they are ensuring a smoother transition into federal oversight while building a competitive advantage. Commercial benefits include unlocking new market opportunities, such as expansion into Europe, attracting new investment, and future-proofing their businesses in a rapidly evolving industry. It’s worth noting that most consumer packaged goods, dietary supplement, and pharmaceutical manufacturers also adhere to GMP and ASTM standards, which means adherence to these standards inherently makes a cannabis operation a more attractive partnership or acquisition target.” The Writing Is on the Wall With over a dozen states already integrating ASTM standards into their cannabis regulations, federal legislation like the CSRA underscores the inevitability of nationwide adoption. This alignment not only standardizes practices but also brings the industry in line with global consumer product regulations. The potential rescheduling of cannabis by the Drug Enforcement Administration (DEA) adds further urgency. Rescheduling would bring cannabis closer to mainstream regulations for consumer products, making compliance with GMPs and ASTM standards essential. A Call to Action for Operators For cannabis and hemp companies, the time to act is now. Implementing GMPs and ASTM standards is no longer a strategic advantage—it’s a necessity for survival in a rapidly evolving market. This applies across the board: Cultivation : Standardized growing practices to ensure consistency and purity. Laboratory Testing : Rigorous protocols to validate product safety and potency. Manufacturing : Adherence to GMPs to maintain quality throughout the production process. Packaging and Labeling : Compliance with new labeling requirements to meet consumer transparency demands. Expert Support Is Available At The GMP Collective, we specialize in guiding companies through the complexities of adopting these standards. Our expertise ensures that your products, processes, and facilities are not only compliant but positioned for long-term success in a regulated market.
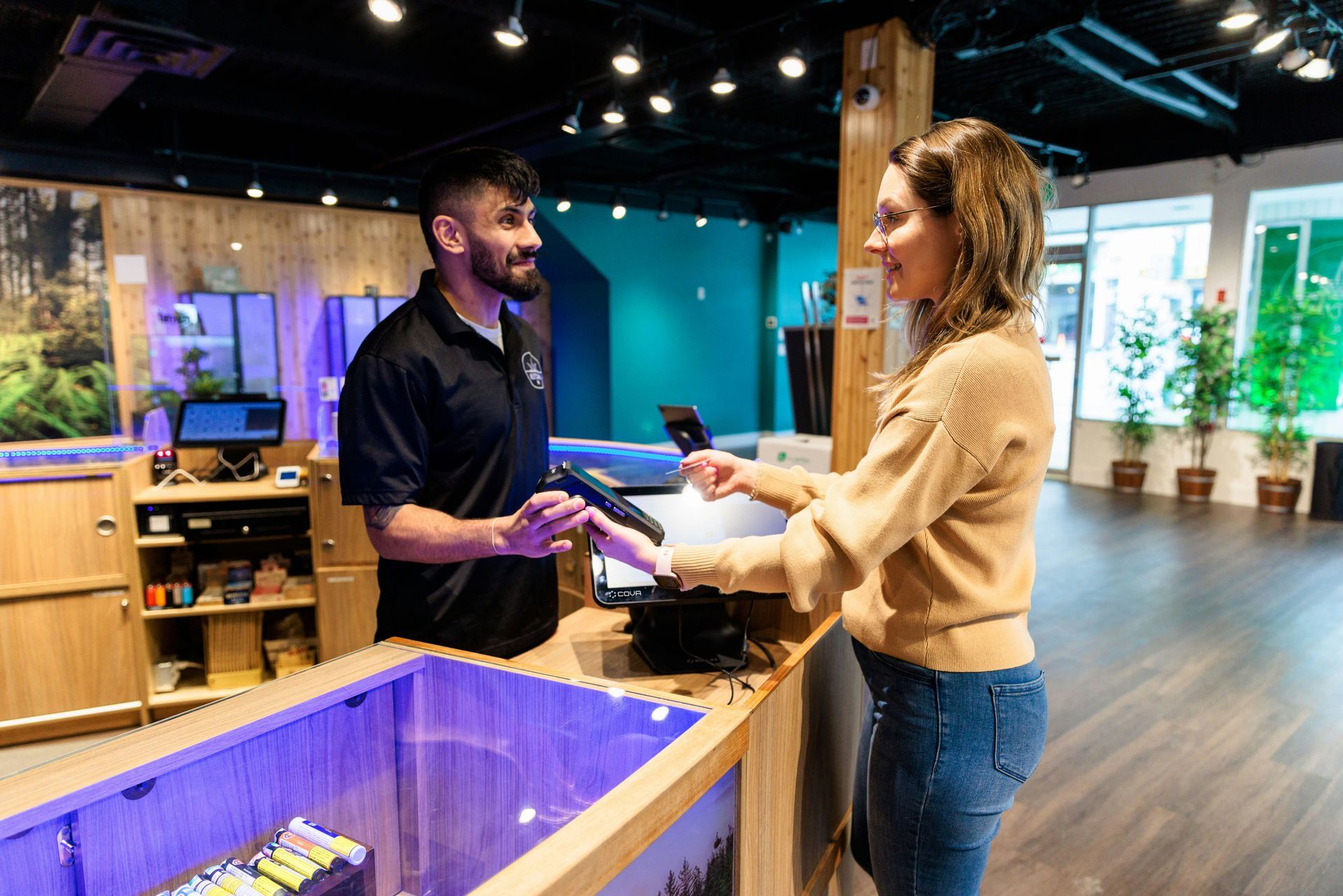
The Prevalence of Consumer Complaints in the Cannabis Industry The legal cannabis market is experiencing rapid growth, particularly in North America. As of August 2024, 25 U.S. states have legalized cannabis for recreational use, and many others allow cannabis for medical purposes. Similarly, Canada's legal market continues to grow since the 2018 legalization. However, as more consumers turn to legal cannabis products, the volume of consumer complaints has risen in tandem. Several factors contribute to this increase in complaints. As cannabis products become more accessible, consumers have higher expectations for product quality, consistency, and safety. Furthermore, the legalization of cannabis has brought in a wider range of consumers, many of whom are less familiar with the potential risks and variability of cannabis products, leading to heightened concerns when products do not meet their expectations. Common Complaints in Legal Cannabis Products Consumer complaints in the legal cannabis market cover a broad spectrum, but some of the most frequent issues include: Product quality concerns : Consumers often complain about the perceived or actual quality of cannabis products. This includes issues like mold, contamination with pesticides, and inconsistency in potency levels. Labeling inaccuracies: Mislabeled products, particularly in terms of THC and CBD content, are a common source of complaints. Consumers are rightfully concerned when the product they purchase does not match the advertised potency or ingredients. Packaging issues: Complaints about cannabis packaging are also common, with some consumers finding the packaging difficult to open, while others raise concerns about its environmental impact. Adverse effects: Unexpected side effects from cannabis products can lead to consumer complaints, especially when the products do not provide adequate warnings or instructions for use. Customer service grievances: Slow response times, poor handling of product returns, or inadequate customer service can also lead to negative consumer experiences. A Case in Point: California’s DCC and Pesticide-Laden Cannabis Products A particularly significant example of the prevalence of consumer complaints in the cannabis industry occurred in California, one of the largest and most heavily regulated cannabis markets in the world. In 2020, the California Department of Cannabis Control (DCC) received a wave of complaints from consumers about cannabis products that were allegedly contaminated with pesticides. These complaints prompted an investigation by the DCC, which ultimately led to the discovery that several cannabis producers were using illegal pesticides in their cultivation processes. The investigation revealed that multiple batches of contaminated cannabis products had reached the market, putting consumers at risk of exposure to harmful chemicals. In response to these complaints and the subsequent investigation, the DCC enforced strict penalties on the non-compliant businesses, including product recalls and fines. This case highlights the significant role that consumer complaints can play in uncovering non-compliant practices within the cannabis industry and driving regulatory enforcement. The Impact of Consumer Complaints on Cannabis Operators The rise in consumer complaints poses several risks for cannabis operators, particularly in a highly regulated industry like cannabis. The impact of these complaints can be wide-ranging, affecting everything from a company's reputation to its bottom line. Reputational Damage In today’s digital age, consumers have more avenues than ever to share their experiences and voice their concerns. Social media platforms, cannabis review sites, and online forums are filled with consumer feedback, both positive and negative. Reddit, for example, seems to be a popular forum for cannabis product feedback. When complaints about product quality or safety arise, they can quickly spread across these platforms, damaging a brand's reputation. For cannabis operators, negative reviews can have long-lasting effects on customer loyalty. Consumers are likely to steer clear of brands that have been associated with safety issues, poor quality, or negative experiences. In an industry as competitive as cannabis, where brand differentiation is key to success, maintaining a positive reputation is crucial. Cannabis is still a relatively nascent industry and as such many brands haven’t yet built a foundation of credibility quite yet, which means that a) product complaints can really set you on the back foot without brand equity to fall back on but it also means b) there is an opportunity to build consumer loyalty from your response to complaints . Easier said than done, we will explore this in more detail shortly. Regulatory Implications Cannabis operators are subject to stringent regulations, and failing to address consumer complaints can lead to serious regulatory consequences. In the United States, for example, the Food and Drug Administration (FDA) has issued warnings to several companies selling cannabis-derived products (particularly CBD products) due to consumer complaints about mislabeling or false claims about product benefits. In cases where complaints reveal violations of regulatory standards, cannabis operators may face penalties such as fines, product recalls, or even the suspension of their licenses. The DCC example mentioned earlier demonstrates the regulatory risks operators face when they fail to address quality issues brought to light by consumer complaints. Financial Losses Consumer complaints can also have a direct impact on a company’s finances. Negative experiences can lead to lost sales, as dissatisfied customers choose not to make repeat purchases. In addition, when complaints result in product recalls or regulatory penalties, the financial costs can be substantial. Companies may need to halt production, issue refunds, or invest in corrective actions, all of which can strain their resources. The Formula for Handling Complaints: Compliance x Speed x Resolution x Reporting = Success The Importance of an Expedited Complaint Response Process Given the potential consequences of consumer complaints, it is essential for cannabis operators to respond quickly and effectively. A slow or inadequate response can exacerbate the problem, turning a small issue into a larger one. Building Customer Trust and Loyalty One of the most important reasons for addressing complaints quickly is the impact it can have on customer trust and loyalty. When consumers feel that their concerns are being taken seriously and that the company is committed to resolving the issue, they are more likely to continue purchasing from that brand. In contrast, a slow or dismissive response can drive customers away, leading to lost business and negative word of mouth. Mitigating Legal and Regulatory Risks For cannabis operators, speed is not just about customer satisfaction—it’s also about compliance. Regulatory bodies like the FDA, Health Canada, and the DCC require companies to respond to complaints in a timely manner. Failing to do so can lead to investigations, fines, and other penalties. By establishing a robust complaint response process, operators can reduce the risk of regulatory action and ensure they remain compliant with industry standards. Reducing the Risk of Escalation A swift response to consumer complaints can prevent small issues from escalating into larger problems. For example, a complaint about mislabeled THC content can be resolved through a refund or product replacement, but if left unaddressed, it could lead to regulatory scrutiny, fines, or a full product recall. Addressing complaints promptly can help operators resolve issues before they spiral out of control. Operational Efficiency Handling complaints efficiently can also improve overall operational efficiency. By addressing issues quickly, operators can identify potential problems in their production or supply chain early, allowing them to make necessary adjustments before more products reach consumers. This proactive approach can lead to better quality control, fewer recalls, and a more streamlined operation. Leveraging eQMS Solutions for Complaint Handling One of the most effective ways for cannabis operators to manage consumer complaints is by leveraging electronic quality management systems (eQMS), like C15 Solutions . These digital tools can streamline the complaint handling process, ensuring that issues are addressed quickly and compliantly. Automating Complaint Receipt & Tracking An eQMS streamlines the process of receiving, logging, tracking, and resolving complaints. By centralizing complaint data in a digital system, operators can ensure that all complaints are documented and addressed in a timely manner. Automated tracking also allows for greater transparency, making it easier for operators to monitor the status of complaints and confirm timely resolution.
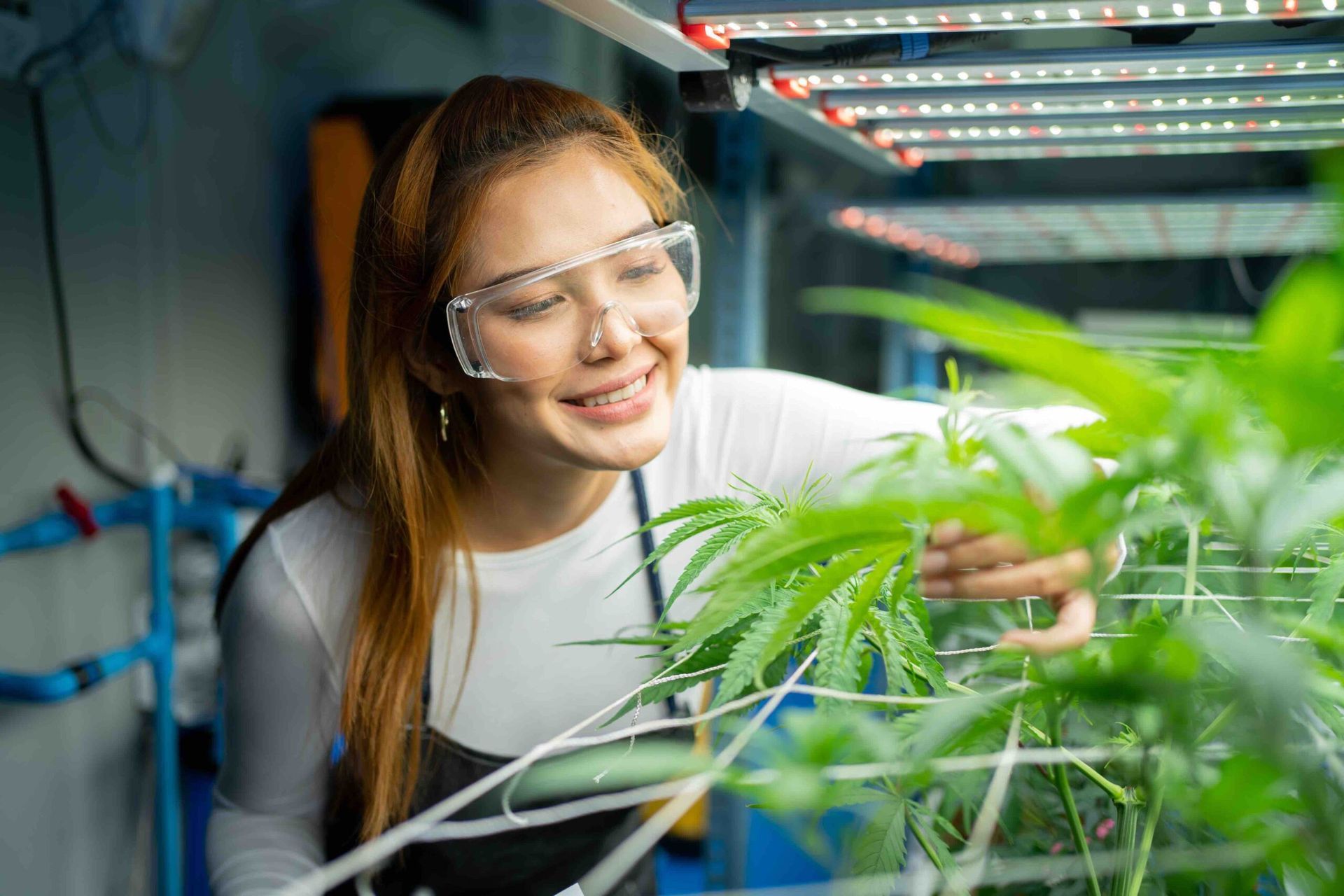
Employee Health & Safety (‘EHS’) is becoming an increasingly important topic in the cannabis industry. The Occupational Safety and Health Administration (‘OSHA’) is a vital agency within the United States Department of Labor. Its primary purpose is to ensure safe and healthy working conditions for employees by setting and enforcing standards and by providing training, outreach, education, and assistance. Unfortunately, back in 2022 there was a significant incident involving an employee's death from inhalation of ground cannabis dust at a Multistate Operator (MSO) facility. Reports, in the public domain, show OSHA investigators found the employee died from occupational asthma due to exposure to ground cannabis. One finding was that workers weren't provided enough information and training on the hazards involved in the production and grinding process. This incident illustrates the significance of both everyday hazards inside a cannabis facility as well as the responsibility of cannabis companies to prevent these incidents from occurring. In this blog, we will outline typical hazards as well as tools to assist cannabis operators in responding to OSHA inspections or similar agencies in other jurisdictions such as CCOHS (Canada) and EU-OSHA (Europe). To give you an idea of the scope of OSHA, the org., along with its state partners, operates with approximately 1,850 inspectors responsible for the health and safety of 130 million workers across more than 8 million worksites. This ratio equates to about one compliance officer for every 70,000 workers. In fiscal year 2023, OSHA conducted a total of 34,267 federal inspections ( OSHA ). Within the cannabis industry, it has been observed that OSHA's involvement is likely to increase as the industry becomes more mainstream. This is particularly true in states like Colorado, where cannabis cultivation has become a significant industry. OSHA violations and fines, while not commonplace in the cannabis space, are expected to become more frequent, especially regarding issues like pesticide use in cultivation operations. To be very clear, despite the cannabis industry’s status as a federally illegal industry, it is very much still responsible for adhering to and complying with OSHA regulations ( https://mjbizdaily.com/osha-intervention-cannabis-industry-qa-jolene-donahue/ ). The power of OSHA investigators ranges from fines to even stop work orders. Investigators have actual fact-finding powers under the laws and if, as an employer, you can not prove the actual facts on the ground at the time of any incident, then there is little power to mitigate the OSHA fact findings.
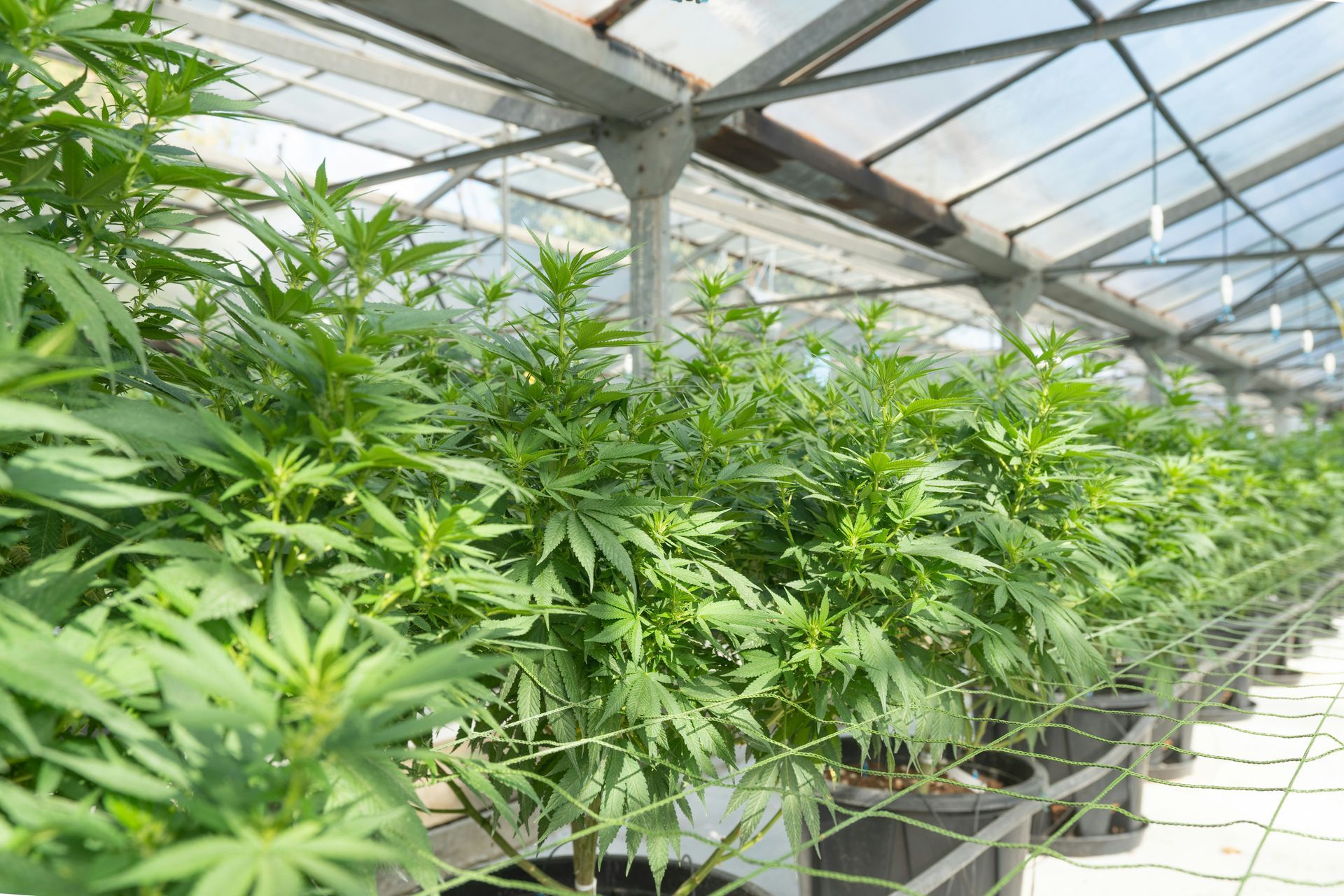
Introduction Welcome to the dynamic world of the cannabis industry, where the quality of the final product is much more than meets the eye. In this blog, we're going to explore what really goes into making elite cannabis. For the purpose of this blog, we’re going to deconstruct ‘quality’ into two forms – front-end quality (consumer facing attributes) and back-end quality (production ®gulatory attributes). At a high-level, we can think of front-end quality as how it smokes/affects us, and we can think of back-end quality as the safety & consistency associated with the product. This deconstruction and exploration will take us from the visible traits like the plant's appearance, potency, aroma, and purity to the behind-the-scenes action at the growing facility itself - the regulations, growing techniques, quality processes, and laboratory test results. It's not just about growing a plant; it's about a detailed and careful process that ensures what ends up in your hands is safe, consistent (or at least as consistent as possible) and of the highest standard. In other words, growing high quality cannabis is both an art and a science. Section 1: Front-End Quality First, we’re going to tackle front-end quality. Broadly speaking, front-end quality attributes are perceived more by end consumers. In no particular order, here are the most common front-end quality attributes that consumers typically use to evaluate their product: Appearance → We’ve also heard the term ‘bud integrity’ used to evaluate the appearance of flower. Is the bud whole & dense, or does it have noticeable gaps? Has it been trimmed cleanly or sloppily? The color of the flower is also important – not that any one particular color is better, rather, does the color line up with genes of that particular cultivar? Finally, visual inspection of trichomes will tell a story as well. Generally speaking, the more the better (i.e. more ‘frostier’ looking). That said, an abundance of trichomes doesn’t tell the whole story; are they clear, milky white, or amber-ish/yellow? Clear means the flower may have been harvested too early and hasn’t been properly cured. Amber/gold means the flower was harvested too late and THC degradation has begun. Milky white = just right! Potency → Much could be written here and potency is often subjective, but what is absolutely true is that there is much more than just the stated THC% telling a story here. When it comes to cannabis flower, there will always be an ‘entourage effect’, where many cannabinoids (as much as 100s!) will interact with each other to deliver a specific effect. As the wellness product market develops, consumers may be more interested in minor compounds like CBN or CBG rather than THC. Terpenes may also impact how potent we feel a product is. Bottom line, don’t evaluate the quality of flower on THC % alone. Aroma → Often described as ‘head’ – the only rule of thumb that applies here is, the stronger the better! Much like color however, the aroma of flower should be specific to the genetics it came from. This is also where terpenes come into play. The higher the % of terpenes, the more ‘flavor’ a patient/consumer will taste. Like many front-end quality attributes, aroma is subjective and certain terpene profiles may appeal more to different consumers. Purity → It goes without saying that a contaminant-free product is the desired outcome from a safety and quality perspective. The presence of powdery mildew (or ‘PM’, a white, powdery looking substance on cannabis flower) indicates a serious quality issue. It doesn’t necessarily mean it’s not safe to consume (though we wouldn’t recommend it), but it DOES mean the plant was sick and PM will adversely impact the purity and potency of the plant. Section 2: Back-End Quality There are a LOT of considerations when it comes to back-end quality. For instance, different cultivation techniques can influence flavour, potency and even how the flower smokes. Furthermore, the science of processing can have profound impacts on the preservation or degradation of final derivative products. Without getting prescriptive re: superior cultivation & processing techniques, (indoor vs outdoor, organic vs. non-organic, different post-harvest processes etc.) what we will say is that the formula for back-end quality could look something like genetic potential x grower expertise x quality assurance. Genetics are the blueprint for flower. It goes without saying that bad genetics will seriously handicap your flower right out of the gate. Doesn’t matter how talented your grower is or how buttoned-down your QA team is, poor genetics = poor quality product. Assuming you have good genetics and cultivation expertise (that best suits the facility), there is still the onerous task of building a QA team and implementing QA at the enterprise level. To be clear, QA is very different from QC, which is typically a single step towards the end of production whereby the final product is determined to have met or not met an internal quality specification. This would be considered ‘table stakes’, and is by no means a differentiating factor when it comes to enterprise quality. To get a better understanding of how truly ‘enterprise’ quality assurance can be, we will highlight a few areas which are often overlooked: Preventative Measures → T his includes everything from the selection of genetics to control of environmental conditions (light, temperature, humidity), soil & nutrient management, management of hazards & critical control points, and especially supplier qualification. As cannabis supply chains expand, so to does the risk to quality as one weak link in the chain can adversely impact the end product. Trust is KEY when it comes to supply chain partners. Compliance and Regulations → Authorities and regulatory bodies demand adherence to regulations and audit your processes involving the back end of quality. Some states now have provisions that make having a quality management system in place to do just this. As de-scheduling becomes more of an expectation, this form of oversight will favor those who build brands based on the front and back-end approach to safety and quality. Those that cut corners or believe “quality does not sell” will not have a sustainable brand as regulations evolve. Lab Testing → C onsidered a hot topic today in light of ‘THC inflation’ debates, the burden of testing does not entirely fall on third party testing laboratories. QA are usually responsible for the ‘sampling’ process which can not only influence testing outcomes but can also lead to wider discrepancies between potency claims made on a label, ultimately leading to customer dissatisfaction when they are not getting the product consistency they desire. This is especially true for medical patients that may sometimes require specific levels of potency. Furthermore, regardless of COA pass/fail results, QA teams should be tracking test results for individual analytes in order to do a proper trend analysis and ensure finished products are meeting their own internal specification as well. This best practice drives product consistency. Section 3: Connecting Front-End and Back-End Hopefully this blog has given you a more complete picture of quality in cannabis. The journey of cannabis flower from seed to consumer is a long one and consumers are often only privy to the post-harvest journey. Back-end quality attributes like genetics selection , along with the strength of your growing and quality assurance teams will absolutely impact the front-end quality attributes that consumers typically ‘grade’ their flower by. Connecting the front end and back-end does not require multiple solutions or confusing array of unintegrated platforms. It does require an approach that aligns the front with the back -end quality brand attributes in an easy and efficient (low cost) manner. Of course, any business is resource-constrained and cannabis is no exception – in fact, one could argue it’s even more resource constrained that other regulated sectors like food & beverage or pharma given the tax burden and relative nascency of (constantly evolving) cannabis regulations. As such, it’s important to be as innovative as possible when it comes to managing the back-end of your operation. Here is a shortlist of some examples of innovations in cannabis QA: Advanced Analytical Testing Techniques → Advances in next-generation sequencing as well as spectroscopy and chromatography allow for more frequent and comprehensive testing Cultivation & Harvesting Innovations → Automated climate control & monitoring systems as well as leveraging data analytics via IoT sensors ensures real-time quality management + better informed decision making Digitized Quality Management Systems → D igitizing and automating an entire Quality Management System will save massive amounts of time all the while ensuring adherence to internal controls and external regulations alike. This results in a more compliant and more consistent product. Furthermore, using a system like C15 Solutions that comes ready to integrate into complimentary systems like your ERP , S2S , environment controls , or even LIMS enables an operation to achieve true ‘enterprise’ quality assurance, while dramatically lowering associated production costs like waste, re-work, audit observations/penalties, recalls, etc. A brand needs to build trust in the consumer and this best comes from holding front-end and back-end standards to the level of your brand attributes. We encourage readers, be they facility managers, budtenders or consumers, to start asking more back-end quality questions to get the complete picture of the product they produce, sell or consume. Product education is a big theme for a sector fresh out of prohibition and, in our opinion, back-end quality doesn’t get the attention it deserves!
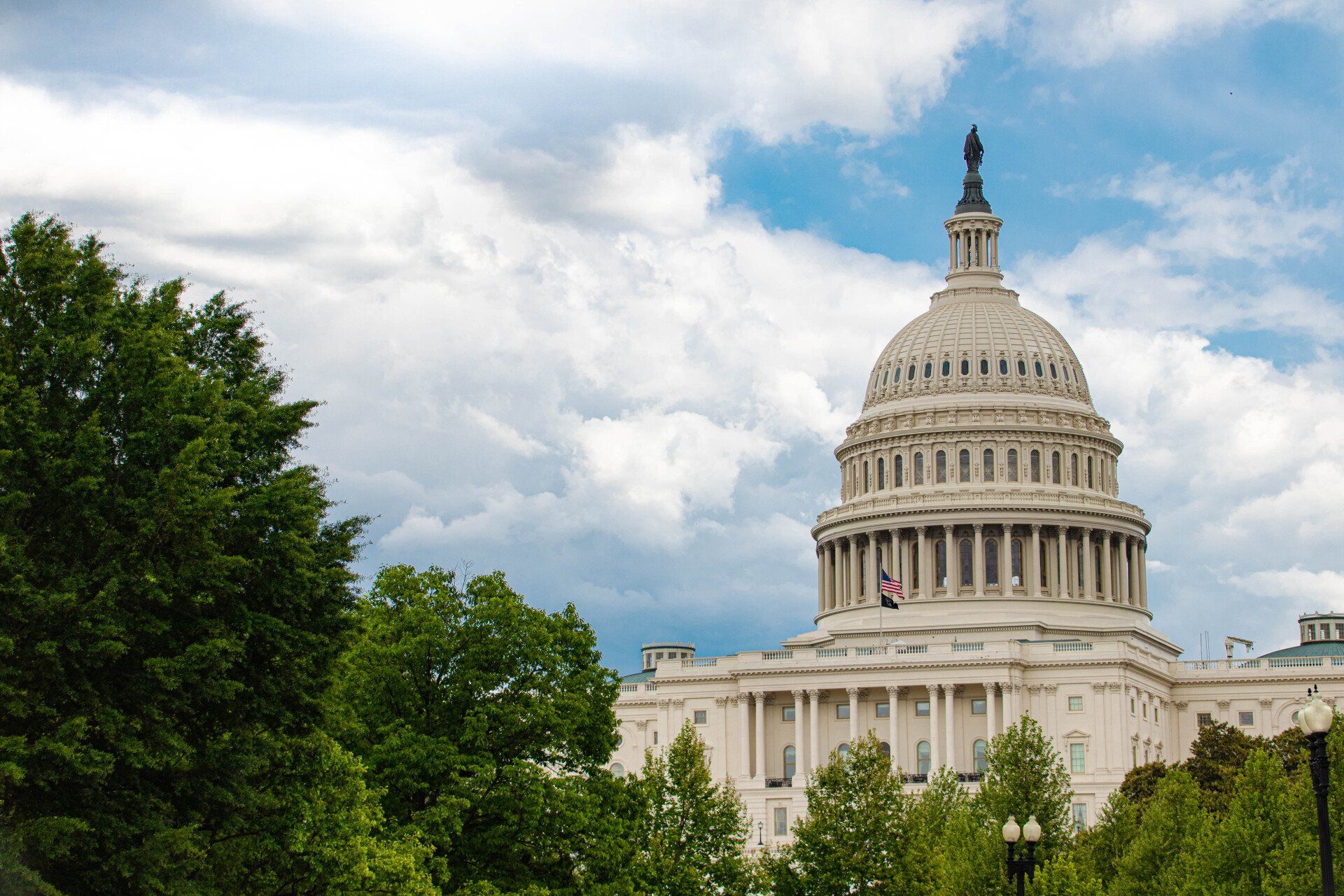
The answer, my friends, is blowing in the wind (Bob Dylan). Almost to a person, the sector would prefer the FDA/DEA to remain out of the regulation of even medical cannabis and would want the full de-schedule option. This is extremely remote since the Department of Health and Human Services (“DHHS”), which houses the Federal Drug Administration (“FDA”), sent a private recommendation to the Drug Enforcement Agency (“DEA”) to reschedule cannabis to category III. Category III means it is less subject to abuse harms than I and II drugs and substances. The Congressional Research Services Report, Sept 13, 2023, stated that the Schedule III category would mean “significant implications for state medical purposes but fewer for state recreational programs.” The report neglected to speculate on what these implications might look like. The report also stated that the DEA, to its knowledge, has never rejected an FDA recommendation on rescheduling.